Well engineered, cost-effective and water-lubricated main guide bearing solutions for rehabilitation project
Originally built in 1922, the Raanaasfoss I Power Plant in Norway recently began a rehabilitation project to update the plant’s performance and render it more environmentally friendly. In keeping with this goal, the plant, now called Raanaasfoss III has been fitted with Thordon SXL water lubricated main guide bearings and segmented shaft seals.
The selection of a water lubricated solution for the lower guide bearing instead of the more traditional oil lubricated design allows the bearing to be lubricated with the same river water which is powering the turbine. This completely eliminates the risk of oil leaking from the bearing assembly, travelling down the shaft past the packing gland and contaminating the turbine’s discharge or tailwater. Not only does converting a turbine from oil to water help protect the environment, it also brings operational and maintenance advantages over the original oil lubricated bearing system.
The series of new turbines, all supplied by Voith Hydro, are to be installed as an extension of the present turbine house. The scope of supply includes six vertical propeller turbines, each with a maximal output of 15.5 megawatts. Commissioning of the first unit was completed in December 2012 and the last unit will be operational by spring of 2016.
Voith Hydro, one of the world’s largest turbine manufacturers, started almost 3 years ago performing a study to evaluate different upgrading possibilities for the old Raanaasfoss power plant. Voith turned to Thordon Bearings for complete turn-key water lubricated main guide bearing assembly.
Thordon was tasked with providing a design solution for the whole assembly using water as the lubricant in the place of oil. The use of water as an alternative to oil lubrication is a long standing area of expertise for Thordon with their non-metallic bearings in operation in the hydro industry for over 30 years. Environmental impact was a concern for the project and Thordon’s water-lubricated bearings seemed to be the right fit for both their technical requirements and environmental mindset.
The bearing design for the Raanaasfoss units focused on providing a fully hydrodynamic bearing design with adequate support to carry the expected loading while integrating Thordon’s unique tapered keyset feature for fixing the polymer bearing directly into the fabricated stainless steel bearing housing without the use of adhesives or additional mechanical fastening. This eliminates the need for a separate bronze bearing carrier while still retaining the ability to replace the split bearing shell without requiring disassembly of the large bearing support housing. The reduction in the complexity and total number of components in the assembly results in quite a substantial savings in cost. The use of the Thordon tapered keyset greatly reduces downtime during bearing inspection or replacement as it facilitates easy removal of the polymer bearing shells without removing the shaft or bearing housing.
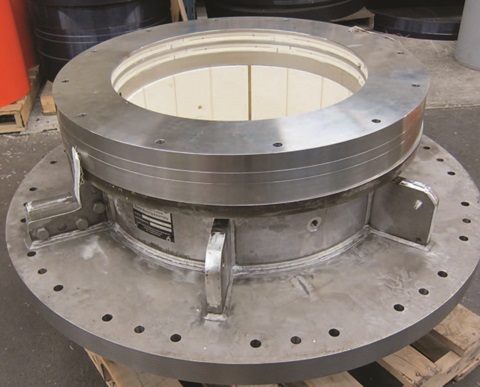
“Our previous experiences with projects of this nature are what helped position us as experts in the field. Our overall design proposal was selected because it met the technical requirements, offered several unique design advantages, and provided an effective way to reduce cost by eliminating a large amount of bronze from the original design,” says, Greg Auger, Business Development Manager for Clean Power Generation at Thordon Bearings. “Turbine designers who choose to use a hydrodynamic water lubricated main guide bearing solution will not only gain environmental advantage over their competitors but can find a cost and technical benefit as well.”
In order to maximize the effectiveness of the lubricating water being delivered to the bearing, the recommendation was made to fit a Thordon SXL segmented shaft seal above the bearing assembly to prevent entry of unfiltered river water into the bearing space. The open-loop design allows the water to be delivered to the top of the bearing, directed down through the bearing space, and then exit directly to the runner. This simplistic yet effective design prevents build-up of abrasives, cools and lubricates the bearing, and maintains a conditioned bearing space to ensure long and predictable bearing life.
Thordon Bearings Inc. designs and manufactures a complete range of polymer bearing and shaftline solutions for the marine, clean power generation, pump, offshore and industrial markets. Thordon’s strong and recognizable global brand is known for high quality and superior performance, eliminating oil and grease from bearing applications in ships, hydro-turbines, vertical pumps and many other industrial applications.